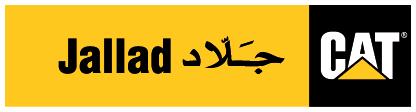
MX350 Controller
The MX350 controller is specifically designed for low voltage Automatic Transfer Switch (ATS) applications. The flexible control and communications options are ideal for any application. Integrated push buttons, graphical controls and LED indicators reduce external components and wiring in addition to providing local control and access to system information. Multiple communication protocols allow simple integration into monitoring and control systems.
Voltage Unbalance on Dropout for Source 1 and Source 2
5 to 20% of nominal
Delay NeutralTransition Time Delays (DT,DW)
0-10 minutes
Control Power
120 VAC
Specification
Value
Voltage Unbalance on Dropout for Source 1 and Source 2
5 to 20% of nominal
Delay NeutralTransition Time Delays (DT,DW)
0-10 minutes
Control Power
120 VAC
Undervoltage Dropout for Source 1 and Source 2
75-99% of nominal
Undervoltage Restore for Source 1 and Source 2
85-100% of nominal
Overfrequency Dropout for Source 1 and Source 2
50.1 - 63 Hz
Source Sensing
120 - 690 VAC +/- 1% of nominal voltage (+/- .05 Hz, +/-.5 A)
Delay for Engine Cool Down (U)
0-60 minutes
Underfrequency Restore for Source 1 and Source 2
45 - 59.5 Hz
Load Control Relay Contacts (2)
0-259 minutes
Overvoltage Dropout for Source 1 and Source 2
105 - 110% of nominal
Voltage Unbalance for Restore for Source 1 and Source 2
4 to 19% of nominal
Storage Temperature
(-40˚C - 90˚C )
Underfrequency Dropout for Source 1 and Source 2
45 - 59.9 Hz
Overfrequency Restore for Source 1 and Source 2
50 - 62.9 Hz
Delay Transfer to Nonpreferred Source (W)
0-5 minutes
Operating Temperature Ambient
(-20˚C to 50˚C)
Communications Interface - Optional
Serial RS-485 upt to 115.2 Kbps or TCP/IP (10/100 base-T)
Overvoltage Restore for Source 1 and Source 2
103 - 108% of nominal
Load Control Relay Contacts (1)
rated for 10A @ 24VDC or 120VAC
Specification
Value
Rating Range
Switch Dependent
Transfer Type
Application Dependent
Switch Type
Application Dependent
- Dual Communications
Built-in RS-485 serial and 10/100 base-T Ethernet
Open protocols - Modbus RTU and Modbus TCP - Available to support Open, Closed and Delayed Transition
- Small footprint
- Graphical control panel
- Multiple communication protocols
- ¼ inch VGA color graphical display with embedded HELP menus
- Status LED's indicating:
ALARM - indicating a problem with the ATS or a user configured alarm condition is active
TD DELAY - indicating the controller is timing before taking the next control action
XFER INHIBIT - indicating the controller will not transfer to the other source without operator intervention
SOURCE 1(S1) AVAILABLE LED - indicating power is present per user setpoints
SOURCE 2 (S2) AVAILABLE LED - indicating power is present per user setpoints
SOURCE 1 (S1) STATUS LED - indicating load is connected to S1 power
SOURCE 2 (S2) STATUS LED - indicating load is connected to S2 power - User-Configurable setpoints for inputs and Outputs
- Field modification of control features
- Plant exerciser clock for 1 day, 1 week, 14 days, 28 days or 365 days. The time base of 365 days permits up to 24 events to be scheduled and the other time bases permit up to 24 events.
- SYSTEM TESTS
Fast Test - test with load, no time delays
Transfer Load - test with load with time delays
No Transfer - test without load, generator start only - Controller Power Supply utilizing the Universal Transformer Assembly (UTA) - provides 170Vdc to the controller and 24Vdc ungrounded to the power relays. The UTA also provides line voltages from 120Vac to 600Vac via an internal six position jumper array, 120Vac UPS input and 24Vdc input battery options.
- Dual processor based with dedicated processor for high speed Serial or Ethernet connections
- All signal in / out relays are isolated via DIN Mounted relay / terminal blocks
- Elevator pre-signal contacts
- Power quality metering
- Elevator pre-signal