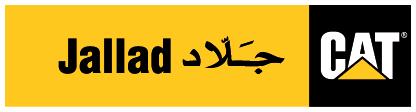
MX150 Microprocessor Controller
The MX150 microprocessor is standard with the CTG product family. The MX150 microprocessor panel controls the operation and displays thes tatus of the transfer switch's position, timer sand available sources. As an embedded digital controller, the MX series offers high reliability and ease of unattended operation across a range of applications.
Rating Range
Switch Dependent
Transfer Type
Application Dependent
Switch Type
Application Dependent
Specification
Value
Rating Range
Switch Dependent
Transfer Type
Application Dependent
Switch Type
Application Dependent
Specification
Value
Undervoltage Dropout for Source 1 and Source 2
75-98% of nominal
Undervoltage Restore for Source 1 and Source 2
85-100% of nominal
Underfrequency Dropout for Source 1 and Source 2
88-98% of nominal
Underfrequency Restore for Source 1 and Source 2
90-100% of nominal
Delay for Engine Cool Down (U)
0-10 seconds
Delay Transfer to Nonpreferred Source (W)
0-5 minutes
Delay NeutralTransition Time Delays (DT,DW)
0-10 minutes
Storage Temperature
(-30˚C - 75˚C ), -22˚F - 167˚F
Operating Temperature Ambient
40 - 400 amp molded shell (-20˚C to 65˚C) , -4˚F to 149˚F
40 - 4000 amp all others (-20˚C to 60˚C), -4˚F to 149˚F
40 - 4000 amp all others (-20˚C to 60˚C), -4˚F to 149˚F
- Digital timer and adjustments with 1 second resolution
- Long lasting LED indicators and an easy-to-view LCD display
- Inputs optoisolated for high electrical immunity to transients and noise
- Digital voltage and frequency adjustments with1% resolution
- Voltage and frequency sensing includes:
–Voltage imbalance detection between phases
–Under frequency sensing on source 2
–3 Phase under voltage sensing on source 1(S1)
– Normal and single phase sensing onsource (S2)
– Emergency - Modular pre-signal option easily integrated into the system (e.g. elevator pre-signal and motor load disconnect)
- Universal Motor Disconnect (UMD) available for programming to pre-signal, post-signal or both
- Line voltage transients are isolated from the control board using remote transformers
- Simplified major components and modules for easy replacement
- On-board diagnostics including voltage frequency, control and timing
- Nonvolatile memory – battery backup not required during normal source outage
- External communication available through LonWorks/ModBus network interface (RS232,RS 422, and RS 485 are also available)
- Maintained and momentary test positions are available to the controller
- Test mode allows manual bypass of all transfer timers when applicable
- Automatic daylight savings adjustment available
- LEDs for continuous monitoring of switch position, source availability, exercise time delay operation and diagnostics
- Simplified adjustment for voltage, frequency and time delay settings
- Close differential 3 phase under-voltage sensing of source 1, factory standard setting 90% pickup,80% dropout (adjustable); under-frequency sensing of the source 1 factory setting 95% pickup (adjustable)
- Voltage and frequency sensing of source 2,factory standard setting 90% pickup voltage,95% pickup frequency (adjustable)
- Test switch (fast test/load/no load) to simulate normal source failure – automatically bypassed should source 2 fail