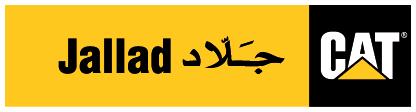
R1700 XE (Battery-Electric)
What if you could have the class-leading payload and superior productivity of the proven Cat® R1700 underground loader without the engine heat or exhaust emissions? You can. Introducing the R1700 XE battery electric LHD—a high-productivity, zero exhaust emission loader with the industry’s only onboard battery. It charges quickly—in less than 20 minutes when paired with two of the durable and mobile Cat MEC500 chargers. This provides an alternative to expensive static charging station infrastructure, as well as the need for additional batteries, battery handling and battery swapping. The machine also features Auto Dig for optimized loading and is factory-ready for autonomous operation. And it delivers the powerful performance, maximum uptime and low operating costs you demand.
Bucket Capacities
5.7-7.5 m³ (7.5-9.8 yd³)
Nominal Payload Capacity
33069 lb
Operating Mass
107460 lb
Specification
Value
Bucket Capacities
5.7-7.5 m³ (7.5-9.8 yd³)
Nominal Payload Capacity
33069 lb
Operating Mass
107460 lb
Shipping Weight
114460 lb
Breakout Force - Lift and Tilt
53330 lb
Static Tipping Load - Straight Ahead - Lift Arms Horizontal
108500 lb
Static Tipping Load - Full Turn - Lift Arms Horizontal
89600 lb
Ride Control
Yes
Specification
Value
Lift/Tilt System - Circuit
Electro – Hydraulic, Positive Flow Control, Flow Sharing
Lift/Tilt System - Pump
Variable Flow Piston/Hydraulic Load Sense
Maximum Flow
78.5 gal/min
Relief Valve Setting - Main
4932 psi
Lift Cylinder - Bore
7 in
Lift Cylinder - Stroke
33 in
Tilt Cylinder - Bore
8 in
Tilt Cylinder - Stroke
22 in
Specification
Value
Raise
6.8 s
Dump
3.3 s
Lower, Empty, Float Down
2.9 s
Total Cycle Time
13.2 s
Specification
Value
Rated Power - Peak
335 HP
Rated Power - Nominal
295 HP
Motor Type
Switched Reluctance
Rated Torque (peak, nominal = @ 12 km/h [7.5 mph] and nominal power)
3200 N·m/660 N·m (2360 lbf-ft/443 lbf-ft)
Efficiency
95%
Cooling Method
Liquid
Ability of Regenerative Braking
Yes
Service Interval
12,000-13,000 hours
Specification
Value
Rated Power (peak, nominal)
303 HP
Motor Type
Switched Reluctance
Rated Torque (peak, nominal = 1,600 equivalent rpm)
600 N·m/531 N·m (443 lbf-ft/392 lbf-ft)
Efficiency
96%
Cooling Method
Liquid
Service Interval
12,000-13,000 hours
Specification
Value
Inverter Rating
350A (nominal DC), 715VDC
Cooling Method
Liquid (coolant)
Component Ratings
IP67, IP69K
Service Interval
12,000-13,000 hours
Specification
Value
0% Grade - Loaded
11.2 mile/h
0% Grade - Unloaded
11.2 mile/h
5% Grade - Loaded
9.2 mile/h
5% Grade - Unloaded
11.2 mile/h
10% Grade - Loaded
5.3 mile/h
10% Grade - Unloaded
6.9 mile/h
15% Grade - Loaded
3.8 mile/h
15% Grade - Unloaded
4.9 mile/h
20% Grade - Loaded
3 mile/h
20% Grade - Unloaded
3.9 mile/h
Specification
Value
Battery Chemistry
Li-lon
Battery Monitoring
With integrated Caterpillar controls systems
Pack Voltage - Nominal
715 V
Pack Energy Capacity - Total
213 kWh
Charging Method
Ultra Fast Charge Onboard
On Board Fast Charging Charge time (0-100%)
Less than 20 minutes (two MEC500 in parallel); Less than 30 minutes (one MEC500)
Battery Cooling Method
Chilled Liquid (Extended Life Coolant)
Operating Temperature Limits (ambient)
50° C/–20° C (122° F/-4° F)
Charging Current, Voltage
1160A (output), 820VDC
Maximum Charging Rate
840 kW (two MEC500 chargers)
Minimum Charging Rate
500 kW
Charging Rate
Up to 4C (matched with MEC500 chargers)
- Improvements in visibility, with lighting and camera coverage, including optional rearview camera with color display, and standardized LED lights that provide illumination to the front and rear.
- Factory-ready for fire suppression, dedicated canister area and multiple fire suppression activation points, including from within the cab.
- Improved access and egress with anti-slip tread on all walking surfaces, newly redesigned handrail system with full coverage and two emergency exits.
- Operator Present System, which protects the machine and operator from uncontrolled machine movements, with hydraulic system neutralization and door sensor.
- Safer service with integrated lock-out/tag-out points, front linkage pins for locking the lift arms in place, and bolt-on tow hooks.
- Completely redesigned cab with more space, with operator seated lower to improve ride quality and head room; adjustable padding for the operator’s knees; and additional foot-space during pedal operation.
- Climate control standard with pressurized enclosed option; all new HVAC coverage with improved airflow, greater defrosting coverage and reduced noise levels.
- Improved ergonomics on all controls, easy-to-use joystick controls, and an isolation-mounted cab to reduce vibration transfer to the operator.
- Optional dual pane windows for reduced noise and improved temperature control in extreme ambient conditions
- Confidence-building features such as continuously variable speed control and implemented virtual gears for machine controllability; automatic retarding controls for maintaining speed on grade; anti-rollback feature; smoother directional changing, with no driveline or powertrain shock loads; and programmable speed management, which improves operator efficiency and reduces fatigue.
- 20% capacity increase from previous models, making the R1700 XE a true 15-tonne (16.5-ton) loader for both load and haul and truck loading applications.
- Fast dumping times — 13.2 seconds to raise, dump and lower — combined with an 18-kph (11 mph) top speed and new traction control system for reduced cycle times, more material moved and lower cost per tonne.
- Excellent machine balance and new electrohydraulic braking system that aid load-and-carry cycles.
- State-of-the-art hydraulic system that delivers 65% more lift force than previous versions and 24,190-kg lift and tilt breakout.
- Features that deliver excellent responsiveness, such as Auto Dig, which automates loading of the bucket; and pilot-controlled steering system to provide more acute feel in tight spaces.
- Proven switched reluctance (SR) electric drive system that is Caterpillar designed, integrated, validated and supported for reliability, ease of cooling and high performance.
- Proven and durable system battery system for fast charging and high output, with Caterpillar engineered cooling system that maximizes performance and battery life.
- Electrical safety built into every level of the battery system, with multiple layers of redundancy and testing to global standards.
- Industry-first onboard batteries, which maximize available run time and provide an alternative to expensive static charging station infrastructure, as well as the need for additional batteries, battery handling and battery swapping.
- Can be fully charged in 30 minutes, or in 20 minutes using dual Cat MEC500 Mobile Equipment Chargers.
- Industry-first standalone Cat MEC500 Mobile Equipment Charger that can be towed, dragged or fork-lifted — eliminating the need for expensive static charging infrastructure.
- Charges quickly, with high power output (300-1,000 volts) and the ability to be used alone or in tandem for optimized charging; boosts voltage to accommodate variable input voltages and offers an adjustable output current that can be used to trickle the charge.
- Connects wherever there is mine power, and two units can charge in parallel with a single transformer.
- Equipped with multiple safety protocols with ground fault monitoring, continually regulating and protecting during the charging process.
- Designed for challenging conditions, with rock fall protection, rated for water and dust, key components mounted against vibration and seismic activity; and sealed against humidity with enclosed air conditioning.
- Newly patented bucket design that offers load path management for long wear life, increased throat angle for easier loading in rock, improved tire coverage for cleanup and tire protection, added strength to match improved breakout force, and added stiffness to inside torque tube for torsional rigidity.
- Five bucket options, including four dump and one bolt-together option — all designed and manufactured to match their performance capabilities.
- Welded, bolted or hammerless Ground Engaging Tools (GET) to meet site-specific needs and fit with site maintenance strategy.
- Bolt-On Half Arrow (BOHA) GET for bucket edges, which offer more wear material than standard weld-on GET and feature a bolt-on design that enables fast and easy removal and replacement.
- New Durilock Lip Shroud system that features hammerless installation and maintenance-free retention of GET, with three interchangeable shroud styles to meet specific applications.
- Front frame section with four-plate design that offers new, fully integrated front axle support casting that absorbs greater impact, vibration and tram loads that come with the growth of the machine capacity and weight.
- Increased axle housing thickness for abrasion protection and corrosion resistance.
- Visibly stronger lift arms with additional steel thicknesses, to ensure extreme loads encountered during loading and tramming are efficiently dissipated for long service life.
- Frame, powertrain, engine and components that are built to be rebuilt.
- ECMs located in single, air-cooled and sealed box located on the service platform of the machine.
- Redesigned hitch with simplified hydraulic routings and more space for technicians to work and clean.
- Modular components that can be removed from the machine and slotted back into place as a single unit, allowing the machine to get back into service much more quickly.
- Improved service access, with swing-open radiator guard, and filter and key service tasks grouped into centralized service section with oil coolers and batteries located just below.
- Electric drive system with fewer moving parts and extended maintenance intervals; sealed electrical connectors, which lock out dust and moisture; and added remote mounted test ports for testing and troubleshooting.
- Factory-ready for remote operation and can be equipped with the industry-proven Cat® MineStar™ Command for underground, which offers line-of-sight remote control; teleremote operation; co-pilot, which requires only directional input from the operator; and fully autonomous operation.
- High-resolution dash displays with 11 language options for access to real-time system information.
- In-cab health monitoring visible on the digital display and monitored through the Cat Product Link™ Elite (PLE) system, including integrated MineStar Health offerings that enable proactive maintenance services and predictive equipment analysis.
- Optional MineStar Fleet for underground, which provides real-time visibility to cycle time, payload, machine position and other key operational parameters.
- Optional MineStar Detect, which uses a proximity detection system coupled with a revolutionary communications and tracking network to prevent incidents and track people and machines in real time.
- Battery electric power, which produces zero exhaust emissions, significantly less heat, less vibration, reduced noise and a better working environment.
- Ongoing research and development into engine compatibility with diesel fuel blended with lower-carbon intensity fuels such as biofuels and renewable fuels.
- Cat Rebuild and Cat Reman programs, which preserve raw materials, conserve energy and reduce emissions.
- Retrofits and upgrades for older machines — to incorporate efficiency improvements and emission reductions, and to keep them in production longer to conserve energy and minimize the need for raw materials.